Ministry of Environmental Protection issues textile water pollution emission standards
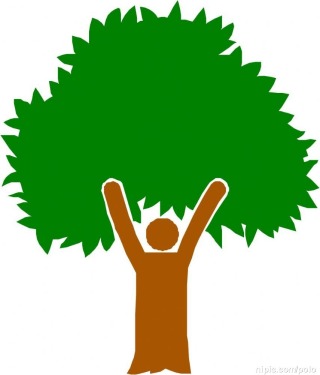
The person in charge of the Department of Science and Technology Standards of the Ministry of Environmental Protection stated that the implementation of the new standard will increase the environmental protection threshold for the textile industry, help reduce the discharge of water pollutants, and promote the sustainable and healthy development of the textile industry. “The implementation of the four standards will effectively promote the reduction of pollutants in the textile industry. After the existing enterprises implement and reach the second phase of the emission limits, the emission of pollutants will be greatly reduced, including chemical oxygen demand and ammonia nitrogen. Compared with 2010, the reduction ratio is expected to reach 68% and 70%, respectively, and the environmental benefits are significant."
Pollution is still the fourth-largest number of emissions in the industry. According to the person in charge, China is the world’s largest textile production and processing base. At present, China’s output of major products such as cotton yarn, cotton cloth, woolen cloth, silk fabrics, chemical fiber products, and apparel are all Ranked first in the world, is a big country in textile production and processing. In 2011, the total industrial output value of enterprises above the scale of textile industry was 3349.1 billion yuan, accounting for 3.9% of the country's total industrial output value. However, at present, China's textile processing is still dominated by medium and low-end products, and the added value of products is relatively low, while enterprises are mainly small and medium-sized. The level of production technology and technological innovation capabilities need to be further improved.
In recent years, due to the development of new products, new dyes, and new processes, while the quality, production efficiency, and water-saving efficiency have increased, the concentration of pollutants in the textile industry's wastewater has also increased dramatically, and environmental protection issues have become increasingly prominent. According to statistics, in 2010, the chemical oxygen demand and ammonia nitrogen emissions of the textile industry were 301,000 tons and 17,000 tons, respectively, which accounted for 8.3% and 7.1% of the total industrial emissions, respectively, ranking fourth.
With the acceleration of the construction of a resource-saving and environment-friendly society, higher demands have been placed on the textile industry in terms of energy conservation and emission reduction, elimination of outdated production capacity, and reduction of environmental impact. In order to effectively control the emission of pollutants from the textile industry, the National Environmental Protection “Twelfth Five-Year Plan†clearly stated that it is necessary to increase the elimination of backward production capacity in printing and dyeing and other industries, raise industry pollutant emission standards, and advance chemical oxygen demand and ammonia nitrogen. The total amount of emissions is controlled and the reduction ratio is not less than 10% of the planned target in 2010. At the same time, the newly issued “12th Five-year Development Plan for Textile Industryâ€, “12th Five-year Development Plan for Printing and Dyeing Industry,†and “Admission Requirements for Printing and Dyeing Industry†and other industry plans and policies have also proposed environmental protection for the textile industry. Specific requirements.
The Ministry of Environmental Protection and the General Administration of Quality Supervision, Inspection and Quarantine recently jointly issued the "Emission Standards for Water Pollutants in the Textile Dyeing and Finishing Industry", "Drainage Standards for Silk Recycling Industry Water Pollutants," "Emission Standards for Water Pollutants in the Wool Textile Industry," and "Mashino Industry The four emission standards, such as the Water Pollutants Emission Standards, together constitute the series of standards for the discharge of water pollutants from the textile industry. The new standards will be implemented from January 1, 2013.
The person in charge of the Department of Science and Technology Standards of the Ministry of Environmental Protection stated that the implementation of the new standard will increase the environmental protection threshold for the textile industry, help reduce the discharge of water pollutants, and promote the sustainable and healthy development of the textile industry. “The implementation of the four standards will effectively promote the reduction of pollutants in the textile industry. After the existing enterprises implement and reach the second phase of the emission limits, the emission of pollutants will be greatly reduced, including chemical oxygen demand and ammonia nitrogen. Compared with 2010, the reduction ratio is expected to reach 68% and 70%, respectively, and the environmental benefits are significant."
Pollution or oldest emissions ranks fourth in the industry. According to the person in charge, China is the world’s largest textile production and processing base. At present, China’s production of cotton yarn, cotton cloth, woolen cloth, silk fabrics, chemical fiber products, and clothing are the major products. Ranked first in the world, is a big country in textile production and processing. In 2011, the total industrial output value of enterprises above the scale of textile industry was 3349.1 billion yuan, accounting for 3.9% of the country's total industrial output value. However, at present, China's textile processing is still dominated by medium and low-end products, and the added value of products is relatively low, while enterprises are mainly small and medium-sized. The level of production technology and technological innovation capabilities need to be further improved.
In recent years, due to the development of new products, new dyes, and new processes, while the quality, production efficiency, and water-saving efficiency have increased, the concentration of pollutants in the textile industry's wastewater has also increased dramatically, and environmental protection issues have become increasingly prominent. According to statistics, in 2010, the chemical oxygen demand and ammonia nitrogen emissions of the textile industry were 301,000 tons and 17,000 tons, respectively, which accounted for 8.3% and 7.1% of the total industrial emissions, respectively, ranking fourth.
With the acceleration of the construction of a resource-saving and environment-friendly society, higher demands have been placed on the textile industry in terms of energy conservation and emission reduction, elimination of outdated production capacity, and reduction of environmental impact. In order to effectively control the emission of pollutants from the textile industry, the National Environmental Protection “Twelfth Five-Year Plan†clearly stated that it is necessary to increase the elimination of backward production capacity in printing and dyeing and other industries, raise industry pollutant emission standards, and advance chemical oxygen demand and ammonia nitrogen. The total amount of emissions is controlled and the reduction ratio is not less than 10% of the planned target in 2010. At the same time, the newly issued “12th Five-year Development Plan for Textile Industryâ€, “12th Five-year Development Plan for Printing and Dyeing Industry,†and “Admission Requirements for Printing and Dyeing Industry†and other industry plans and policies have also proposed environmental protection for the textile industry. Specific requirements.
What are the new requirements for the new standard?
Form the industry's entire process environmental control and tighten the emission limit “to better meet the new requirements of the “Twelfth Five-Year Plan†environmental protection work, further increase the intensity of pollution prevention and control work in the textile industry, and summarize the practical experience based on "The Textile Dyeing and Finishing Industry Water Pollutant Discharge Standard" (GB4287-1992) is revised, and it is necessary to newly formulate the water pollutant discharge standards for the reeling industry, wool spinning industry, and linen spinning industry, "said the official.
He told reporters that in the original standard system setting, except for the textile industry, which implements a separate industry-type pollutant discharge standard, reeling, wool spinning, and hemp spinning have all implemented the Integrated Wastewater Discharge Standard. In the Integrated Wastewater Discharge Standard, only chemical oxygen demand and BOD5 have separate provisions for washing hair-washing wastewater and ramie degumming wastewater. The rest of the indicators are all subject to uniform emission limits, which, to a certain degree, cause industry characteristics. Pollutants have not been fully identified, and emissions control is not well-targeted and the differences are hard to reflect.
The newly released four standards comprehensively cover the production and processing of natural fiber textiles in China and form the whole process environmental control of the industry. The textile dyeing and finishing standards mainly control the pretreatment of cotton and the dyeing and finishing processes of cotton, hemp, wool, silk and chemical fiber. The discharge of water pollutants in the silkworm; silk reeling standards, wool spinning standards, and hemp spinning standards mainly control the discharge of water pollutants from silkworm cocoon processed silks into the silk process, the wool-washing process, and the hemp degumming process. “The system setup is more clear and complete, and it is more targeted to the pollution prevention, supervision and management in the industry.â€
In terms of emission control requirements, the new series of standards have also generally increased requirements and strengthened environmental risk prevention. Among them, the newly revised “Emission Standards for Water Pollutants in Textile Dyeing and Finishing Industry†tightened the emission limits of chemical oxygen demand, five-day biochemical oxygen demand, suspended solids, and ammonia nitrogen to a greater degree than the original standards. More stringent special limits for water pollutants have been formulated for environmentally sensitive areas, and indirect emission limits have been set to strengthen the supervision and management of wastewater discharged to public sewage treatment systems.
In view of the production of pollutants in textile dyeing and finishing industries such as printing, dyeing, and bleaching, the new standard retains the characteristics of indicators such as sulphide, aniline, hexavalent chromium, and chlorine dioxide in the original standard, and further tightens the emission limit. At the same time, additional organic halogen (AOX) indicators have been added to enhance the control of toxic and hazardous pollutant emissions and prevent environmental risks. In addition, in order to strengthen the control of the eutrophication of water bodies, new standards have been added to the new standard for total nitrogen and total phosphorus to meet the needs of environmental management.
The newly-developed three standards for silk, wool, and linen are all targeted at the characteristics of various types of fiber production and processing, identify characteristic pollutants, and increase the control requirements for water pollutants to varying degrees.
The person in charge told the reporter that in the new standard, the setting of indicators is more scientific and reasonable, which is conducive to the promotion of pollution prevention and control technology. In the four standards, the reference drainage volume per unit product is set. The setting of this indicator can prevent diluted emissions on the one hand, and on the other hand, it can also effectively promote water conservation for enterprises and raise the level of clean production.
It is worth noting that, in the “Drainage Standard for Textile Dyeing and Finishing Industry Water Pollutants†(GB4287-1992), the maximum permissible drainage volume is expressed by the amount of water discharged per hundred meters of cloth. This allows different widths and thicknesses to be processed. Similar to the limit of product implementation, the newly revised standard is expressed in tons of product displacement.
A Votive Candle or prayer candle is a small candle, typically white or beeswax yellow, intended to be burnt as a votive offering in an act of Christian prayer, especially within the Anglican and Roman Catholic Christian denominations, among others.In Christianity, votive candles are commonplace in many churches, as well as home altars, and symbolize the "prayers the worshipper is offering for him or herself, or for other people."The size of a votive candle is often two inches tall by one and a half inches diameter, although other votive candles can be significantly taller and wider.
Votive candles are made from different types of waxes including paraffin, soy wax or beeswax. There are different grades of wax with different melting points. Paraffin is often mixed with other types of waxes, such as beeswax or vegetable wax. This is done to obtain the rigidity necessary for the type of candle being made. The speed at which the candle burns depends on the composition of the wax. A Taper Candle that sits in a ring-shaped candle holder may have a low melting point and produce little to no oil, whereas a votive candle set in a glass cup may have a very low melting point and turn to oil. Pillar Candles, large candles often with multiple wicks, have their own formula. Soy jar candles tend to have a lower melting point than pillars and votive candles. Candle quality also varies widely depending on the candle maker. The aroma of a lighted Scented Candle is released through the evaporation of the fragrance from the hot wax pool and from the solid candle itself.
Votive Candle
Votive Candle,Votive Candle Holders,Votive Candles Bulk,Glass Votives Candle
Shenyang Shengjie Candle CO.,LTD , https://www.sj-candle.com